Back in the 1970s, my friend Wayne Gillis and I used to do light shows at science fiction conventions. We had the usual panoply of overhead, slide, and custom-made projectors, and a single, very expensive, helium-neon laser from Edmund Scientific. Calling ourselves Light Opera, and later, Illuminatus, we performed at ConFusion conventions in Ann Arbor, Mich., and at the World Science Fiction Convention in 1976, where Robert Heinlein was guest of honor.
Flash forward 30 years, and I get a call from David Bloom, a web marketing/connection guy and awesome keyboardist. Would we like to revive our act and perform with him at Penguicon 7? You betcha, I said, and Wayne and I set about to update our craft, revive our spent youths, and order a bunch of now-inexpensive lasers. Thus Illuminatus 2.0 was born.
Penguicon is a unique convention that mixes science fiction fans with those deep into open source software. Given the open nature of the event, we decided to share our tech with MAKE readers interested in laser displays and soldering.
Instead of a single, monolithic laser device, we went with a bunch of inexpensive units, and as “cheapness” was the watchword for this project, we housed the devices in the cheapest metal boxes we could find, namely, lunchboxen. (Penguicon is a Linux convention, so it’s one box, two boxen). A search of eBay turned up a raft of cool boxen with science fiction themes, and we were on our way.
Project Steps
Assemble the voltage regulators.
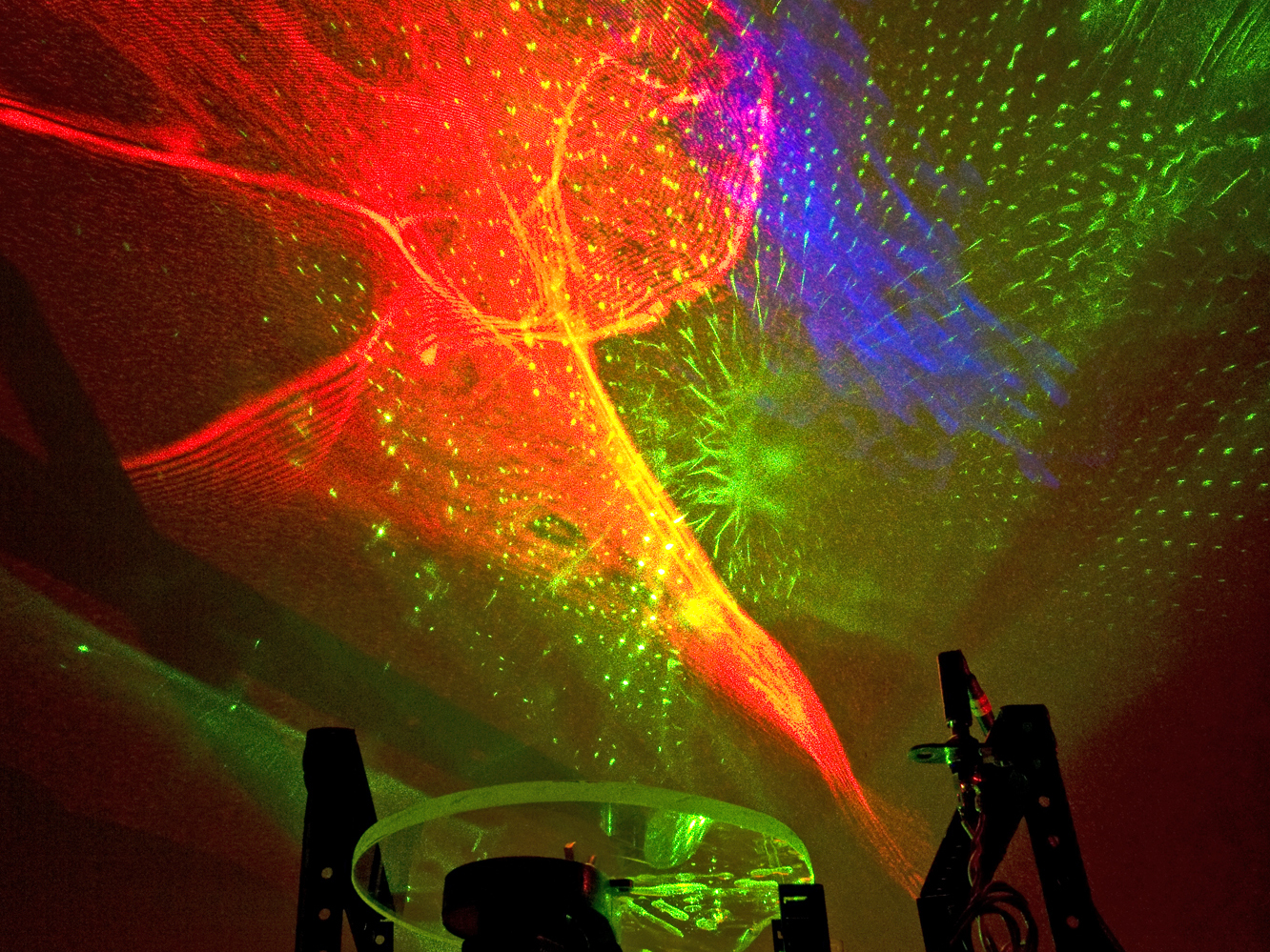
Count the number of voltage regulator circuits you need to build your boxen. Each Lumia box needs 2, a Diffracterator needs 4, and a Motiondizer uses 1.
Cut a section of perf board for each box and follow the circuit schematic in the documents section to assemble its voltage regulator circuits.
If you’re using a laser stronger than 10mW (or want the option to swap one in later), put a heat sink on the LM317 voltage regulator.
Note that all the individual regulator circuits share their connections to power, diode D1, and capacitors C1 and C5.
Make the internal frames.
For each box, start with a base plate made of 3/8″ plywood. Measure the inside of your box at the bottom and cut a piece of plywood to fit, giving it 1/8″ or so of space all around to make removal easier. All the gizmo-ry gets built onto the plate.
Attach side rails to the plate, sized to reach the top corners of the lunchbox. The rails keep everything from falling when the box is on its side, and they also provide places to hang components and serve as convenient handles for removing the workings from the box. I made mine from some erector-set-looking metal stock screwed into ½” blocks of wood glued to the base plate, with the corners secured with pop rivets.
Paint the base plate and rails flat black to prevent random internal reflections.
Now you’re ready to make some laser lunchboxen! Instructions for Lumia, Diffracterator, and Motiondizer follow. The Lumia is a good place to start because it’s the simplest; all you need is 1 laser, 1 motor, 1 lumia wheel, and 2 voltage regulators. For all boxen, the simplest versions use a smaller laser, say in the 5mW neighborhood, which won’t require a heat sink and fan.
Build your boxen: the Lumia.
Make the disk, from plastic or glass. For plastic, glue a washer that fits the motor shaft to the center of a CD spacer. For glass, cut the disk (or have one cut) with a glass cutter and glass drill bit.
In a well-ventilated area, apply model glue or clear epoxy to one surface of the disk, smearing it around with a toothpick to make an irregular surface. These disks can be an endless source of experimentation and amusement as you try different combinations of glue, plastic, glass, and whatnot.
Figure out your component layout on the base plate. If you’re working with a higher-powered laser, leave space for heat sinks and/or fans.
For the motors and laser, position them to minimize footprint and maximize adjustability, so you can fine-tune the beam paths until you get everything dialed in. I usually screw in just one end of the mounting straps, and only screw in the other end after everything is lined up.
With our Lumia device, we used a big 250mW red diode laser from Sunclan (http://clantechlaser.com), so the laser and LM317T regulator are both heat-sunk, with a fan blowing on both. The laser is aimed at a front surface mirror, following the usual configuration, but if your laser is small enough you may be able to skip the mirror and just aim it straight up through the wheel.
Attach everything to the base plate, and adjust. To attach the circuit boards, we used 2 methods. I mounted mine directly to the base plate using wood screws; the plywood acts as an insulator. Wayne mounted his vertically using small angle brackets, which minimizes footprint and provides access to the bottom if you need to tweak the wiring. With pipe straps, you can use the existing perforations for screws, and drill extra holes if the spacing is off.
Assemble the device outside the lunchbox, but periodically put it in to make sure everything fits. As you go along, make sure the laser is happy; warm to the touch is OK, but if it’s burn-your-finger hot, add a fan. Also check that the motor turns at a nice slow speed; <1rpm is best, but adjust to taste.
Finally, attach the lumia disk to the motor, pop it all into your box, and shine on, you crazy diamond!
Build your boxen: the Diffracterator.
Lay out the Diffracterator’s components on the base plate, just as in Step 3. You need to fit 3 motors. I mounted 2 using pipe hangers with long screws through the clamps. Pipe hangers have a smaller footprint than pipe strap and they can hold lasers or motors, as shown here.
Cut the transmission diffractor disk and screw it onto motor 1 with a nut and washer.
Attach the diffraction mirror to motor 2. To make a mounting I bought a ½” length of ½”-diameter nylon spacer (it’s predrilled, so take a motor to the hardware store to choose the right inside diameter), and cut it in half with a hacksaw to make 2 mounts.
I tapped the holes to 8-32 so they screw directly onto the motor shaft, and used epoxy to attach the diffraction mirror to one of the nylon mounts.
Glue the mirror to the end you didn’t cut, to ensure it’s at a right angle to the spacer.
Make the Wobbulator, a plexiglass disk thick and warped enough to dramatically change the direction of the laser beams. I used a 5½” disk of 1″ plexiglass with a hole in the middle, which my glass store cut and drilled for me.
Take the disk out to the garage and have at it with a blowtorch, heating it until it’s soft enough that you can warp a bit of it into a wavy shape, maybe with some bubbles. Then drip a little airplane glue or clear epoxy onto the warped area.
Time for assembly. The Wobbulator takes up the most space, so install it first, screwed onto motor 3, and make sure it clears the side rails.
Remove the Wobbulator and install the reflective diffractor and the laser. Since I used a laser pointer designed for intermittent use, I heat-sunk it by choosing a copper holder and adding copper strip (copper is more thermally conductive than steel).
Add the transmissive diffractor. Hook up the power supply briefly to verify the alignment of everything, holding the Wobbulator assembly in place.
Re-attach the Wobbulator assembly. Note that 2 screws hold it down; this is a heavy piece and it needs the support.
Finally, add the power supply, hook everything up, plug it in, and admire. The magic begins to happen as the warped part of the Wobbulator does its thing, taking you to the Gamma Quadrant and beyond.
Build your boxen: the Motiondizer.
Our box uses a small 5mW red laser. Eventually we’ll beef it up — there’s lots of room here for more mojo and fans to cool it.
Take apart the powered speakers and remove the amp, which is usually a circuit board in one of the speaker enclosures. Note and label the inputs, speaker outputs, and power input, then unsolder the speakers from the amp.
Prepare the speakers. Bend 2 lengths of pipe strap into L shapes, to use as speaker supports; mine needed 3½” each. Epoxy the back of each speaker to a support, removing paint first if needed.
The speaker wire tabs should face up for soldering accessibility, and the base of each L bracket needs room for 2 screws. It also helps to have some extra strap sticking up to use as a handle, and I filed the edges round here, to avoid cutting myself while messing with speaker alignment.
Cover each speaker with a thin rubber membrane, gluing it only around the perimeter. Using silicone adhesive (not model cement) glue a small square of cork to the center of the membrane, and glue a small disk of front-surface mirror to the cork, facing out. If the mirror came covered with protective film, leave it on for now.
Figure out your component layout on the base plate, as in Step 4. Attach speaker C (the one angled up in the pdf) to the baseplate using just 1 screw (you’ll add the second one later once everything is aligned), then bend it back a bit. Similarly attach speaker B (the one the laser will hit) after using a laser pointer to figure out where it should go.
With everything lined up, use a pencil to mark the likely locations of the second screws.
Solder your laser to its power supply and attach it where you held your pointer. I mounted it using a pipe clamp that was a bit wide for the laser, so I tormented the flanges until it fit.
Verify that the beam travels where it’s supposed to and then heads up from the base plate at about a 90° angle. This is an iterative process of tweaking the angles of the laser and both speakers. Once everything lines up, add those second screws to secure the speakers and laser.
Hook up the amp. If your powered speakers run off DC, you can simply use the original stereo input and DC jacks, but to make it neater and more professional we wired these out to 2 panel-mount RCA jacks and a DC jack on the rails. We soldered our jacks to the original jacks’ terminals on the underside of the board. Use shielded cable for the input signal between the RCA jacks and the terminals.
At the DC jack, split the voltage between the amplifier board and the laser’s voltage regulator board. To connect the amp output to the speakers use speaker wire. Observe polarity throughout, +/– and L/R.
If your powered speakers’ wall-wart supplies AC, you need to trace the leads on the circuit board through whatever rectifier diodes turn it into DC, and attach your voltage regulator’s power wires to the DC rails there. If the original wall-wart supplies 8V DC and you’re running on 12V DC, that’s no big deal. Underpowering the voltage regulator is OK. Just don’t overpower it, as this may result in Bad Things like components melting and explosions.
Attach the amplifier and voltage regulator circuit. We screwed the power supply to the base plate, and positioned the amp upright with 2 small angle irons epoxied in place.
If you haven’t already, add the rails (for this lunchbox we did this toward the end, contrary to Step 2).
Drill and mount the power and RCA input jacks to an upper rail; it’s better to put them here than in the box itself, and it preserves the box’s integrity.
Pop the Motiondizer into its lunchbox and test it using any standard stereo output. If it all works, rejoice! Now you can peel any protective film off the mirrors.
Note that this setup wants to see line-level signals from whatever is feeding it.
Conclusion
Open Source Coolarity
Wayne and I have made 5 boxen so far: 2 Lumias (red and red-and-green), a Diffracterator (green), and 2 Motiondizers (violet and green).
And as for Penguicon, things worked very well. The DJ at the dance party wanted to buy a Diffracterator on the spot.
I Sing the Lunchbox Electric
Since the boxen run off batteries, you can do shows in camp. Not that you should, of course.
For indoor gigs, Wayne also built a massive power supply into a project case, and I found a suitable snake cable online that we use to get 12V DC to everything that needs it.
We also have several wall-wart power supplies we picked up at ham fests and such. The boxen don’t draw much power, so a small wart would probably do you. With a couple of warts, we can do shows without having to drag the big box around.
The Wobbulator disk on the Diffracterator, incidentally, is my one contribution to world culture. There are lots of other laser grating effects out there, but AFAIK, this is the first with a Wobbulator. (Although it may have been invented decades ago by Ivan Dryer at Laserium, I dunno.)
Feeding the Motiondizer
The Motiondizer needs full-strength input from your audio system, so if you also want to hear your regular speakers, you may need a splitter such as a distribution amplifier (DA). We use DAs we found on the internet. You can also control the Motiondizer with just a microphone, using a mic pre-amp. In concert, you can run line-level signals for a Motiondizer from the mixing board.
Variations
Lasers are blisteringly awesome to behold, susceptible to endless tweakage, and dirt cheap. The Lumia and Motiondizer boxes have enough room to mount 2 colored lasers, following slightly different paths to create superimposed pattern projections.
The Lumia projector Wayne built (shown here, minus the wheel) has red and green lasers both cooking away. Note the cooling fan and heat sink on the top laser, a 20mW greenie. The mirror is secured with a cabinet door hinge and a strip of pipe strap.
The motor has a more elegant mounting method: standoffs made for circuit board support. He also used ¼" masonite for his base. Having a better stock of sheet metal than I, Wayne used brass strips and small angle brackets for his laser supports. The blue material around the edge is designed to cushion the apparatus in transit, and the copper strip at the top secures the base plate to the box.
RESOURCES
A good place to start: laserpointerforums.com
For advanced users and professional laserists: photonlexicon.com/forums
The pioneering work of Thomas Wilfred: lumia-wilfred.org
Visit makezine.com/20/lunchboxen for hobby laser and materials buying advice and photos of the laser lunchboxen in action.
This project first appeared in MAKE Volume 20, page 110.