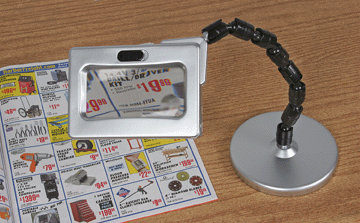
In the twice-monthly Make: Online Toolbox, we focus mainly on tools that fly under the radar of more conventional tool coverage: in-depth tool-making projects, strange or specialty tools unique to a trade or craft that can be useful elsewhere, tools and techniques you may not know about, but once you do, and incorporate them into your workflow, you’ll wonder how you ever lived without them. And, in the spirit of the times, we pay close attention to tools that you can get on the cheap, make yourself, or refurbish.
This week, as part of “Teach Your Family to Solder Week,” we’re looking at what you need to get started in soldering. In Part 1 of this Toolbox, we looked at essential tools. In this installment, we’ll look at some of the support tools that can make soldering more enjoyable, go faster, be less fumey, etc.
We’ve written about the “Dry Solder Tip Cleaners” (aka “Cleaning Genie”) a number of times. They’re sold under different names, but it’s basically a little container of metal shavings that you clean the solder tip in (instead of the damp sponge found on most spring-type soldering stands). Elliot Williams of HacDC writes: “Tip cleaner/tinner is good for rejuvenating oxidized tips, but cleaning your tips with one of these metal sponge thingies makes it almost unnecessary in the first place. Rant #25692: Water rusts/oxidizes metal. Oxidized metal doesn’t transfer heat well. Why the hell would you ever want to touch your soldering iron tip to a sponge with cold water in it?”
You can easily make your own such cleaner by getting a copper scrubby pad at the grocery store and stuffing it into a small container.
A solder dispenser is not really an essential tool, but can come in very handy, especially if you’re doing a lot of near-production-line soldering. Scott Austin, of Dorkbot DC and Dorkbot Baltimore, says: “A larger project of mine (over 60 dip sockets in each of two projects) required lot of soldering. I bought a solder dispenser and borrowed a friend’s soldering station. I was able to solder the sockets (700-800 soldering joints) very quickly with this set-up.”
While we talked about solder suckers and solder braid in the last Toolbox, there’s also the desoldering bulb (which works similarly to the sucker). Scott Austin says: “A desoldering bulb works pretty well. But you do have to work quickly: heating the joint with the iron and then positioning and using the bulb before the solder cools. If you find yourself desoldering a lot, I really like the combination desoldering iron/bulb tool. They’re not that expensive and you don’t have be doing the dangerous juggling between soldering iron and solder sucker.”
When we start talking about soldering tips for soldering (as in ways of improving your soldering, not the tip of the iron), we’ll be talking a lot about clean, clean, clean. It’s one of the keys to successful soldering: keeping the tip of your iron clean, the components clean, the PCBs clean, some argue, even the solder itself. Besides wiping the tip on the stand sponge or metal cleaning “genie,” and tinning the tip (painting some solder on it), you want to clean it off in a chemical tip cleaner periodically to really clean off built-up crud. Multicore is a common brand. Radio Shack has its own brand.
While we’re talking about cleaning, it’s worth talking about scrubby pads. I keep some of these Scotch Brite pads on-hand and use them to “brighten” the copper traces on PCBs before I start soldering. Boards can get fingerprints, dirt, oils, and other gunk on them that can hamper a good solder bond. A quick, gentle clean with one of these can help remove all that.
As I said in the previous column, I lived with a bad iron for far too long. I also lived with a horrible pair of wire strippers (that came with the same el cheapo toolkit). A good pair of strippers makes a world of difference. Above is pair of Paladin 1117 GripP 20 Strippers, which go for $13. To the right is a stripper tool I just got from John Park. He was raving about them, I expressed interest, and being the generous soul that he is, he gifted me a pair. I love ’em! Rather than cutting the insulating jacket on the wire from the side, they cut from the end, pulling the jacket off toward the tool. It just feels like a more natural way to cut and the length of the cut and the tension are fully adjustable. They sell for around $20.
If you’re an old fart like me, your eyesight probably isn’t what it used to be. You can frequently find yourself nose-to-fiberglass with a PCB as you try to see what the heck you’re doing (not that this have EVER happened to me, mind you). You can get florescent lamps with magnifying glasses built into them, or you can go super-cheap and get one of these. Scott Austin bought one of these at Harbor Freight for $6. It’s a 5x magnifier, with a built-in 8x bifocal, three bright-white LEDs, and a flexible shaft. (Maybe if I mention to John Park that I want one… :-)
Just as I vividly remember the difference between going from my crappy 15-watt repair kit iron to a decent Xytronic pencil iron, I remember how amazing the different was when I tried soldering on a fairly expensive soldering workstation — another whole level of easy-of-use, quality, and control. If you decide to take electronics and soldering seriously, you’re going to want to invest in a decent soldering station. This one is the Weller WES-51 ($84 on Amazon). R. Mark Adams, of HacDC/Dorkbot DC, writes: I use the Weller WES-51 and love it. Seriously. More expensive than an el cheapo “houseburner” iron from Radio Shack, but worth every dime. I tell people to get a station like this and a Panavise (see Part 1). With these two items, you can do high-quality work with minimum frustration. I always tell people that you can have both of these tools for less than some people spend on a single golf club, and have way more fun! :-)
I have the Xytronic 456DLX workstation with fume extractor. I got it for $75 from Circuit Specialists (and it came with a free digital multimeter that sucks a lot less than I expected). Overall, I’m happy with it. The cord is long, with a rather thick insulating jacket, so it’s sometimes awkward to figure out how to position the extractor, the soldering stand, the unwieldy cord, and the work so that the cord is not a nuisance.
[Thanks to Becky Stern, Elliot Williams, Scott Austin, R. Mark Adams, Michael Panfeld, Andrew Righter, Katie Bechtold, Alberto Gaitaacute;n, Jay Koby, The Doctor, and everyone else at MAKE, HacDC, and Dorkbot DC who participated in the discussions on soldering tools]
More:
- Toolbox: Soldering essentials, Part 1
- Toolbox: Knives out!
- Toolbox: Shop bookshelf (catalogs)
- Toolbox: Shop bookshelf (mechanics, tools, and misc)
- Toolbox: Shop bookshelf (electronics and MCUs)
- Toolbox: Shop tips and show-offs
- Toolbox: What the hell is that thing?
- Toolbox: Soldering station tools and hacks
- Toolbox: Jigs, clamps, and helping hands
- Toolbox: Ten tools you won’t want to live without
- Toolbox: Benchtop power supplies
- Toolbox: Portable lighting
- Toolbox: Portable workbench
- Toolbox: From “miserable old box” to workshop showpiece
ADVERTISEMENT