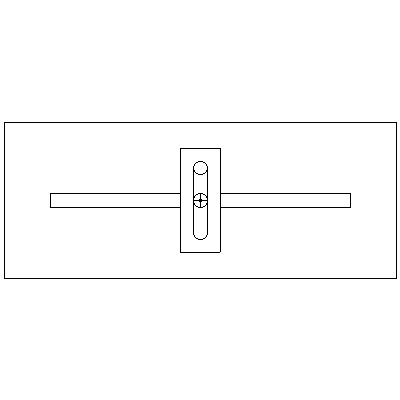
Image by Dbarak [CC BY 3.0]
There are lots of types of actuators on robots. You know, the things that make the robot move and allow it to interact physically with the world … grippers, arms, legs, wheels, etc.
Unlike wheels or servo-driven arms, linear actuators operate by pushing or pulling along a straight line. There are many potential uses for this, from finely positioning an X-Y table for an automated tool to having your robot servant push a door bell button for you when your finger gets tired. Here are five different types of linear actuators you can integrate into a future robot build.
1) Motorized Threaded Rods
You can make a powerful linear actuator with a threaded rod, some matching nuts, and a battery operated drill. Or you could make a very precise one using a stepper motor, which is exactly what you see on many 3D printers.
For a lightweight version, recycle a cylindrical glue stick and use a modified servo and a slide potentiometer, as Gareth from Let’s Make Robots explains in this post and the video below.
2) Pneumatic Cylinders
Pneumatics are a form of fluid control using pressurized gasses, usually air, to apply a force. Pneumatic cylinders are available in a variety of sizes. They are strong, durable, simple mechanisms, with many industrial applications. One advantage of pneumatics is that unlike motors or servos, they can generally hold their position once pressurized, without requiring additional power.
Many FIRST Robotics Competitions allow use of pneumatics, so it is not far-fetched to consider their use in a homemade robot. I recently met a member of Piscataway High School Robotics Team 224, whose forklift robot competes in FIRST competitions. He explained how an onboard compressor pressurizes a storage tank, with regulators to set the working pressures for the cylinders. A pair of cylinders allow the fork’s gripper to open and close, and motors provide lift. The robot could easily pick up and stack plastic storage bins as shown in the picture below.
3) Scotch Yokes
Many robots use motors or servos as actuators, both of which provide rotational motion. You can turn that rotation into a linear motion with a mechanism called a Scotch Yoke. The Scotch Yoke has a rod with a rectangular slot cut in a “yoke” in the middle of it. A pin on a rotating wheel is inserted in the slot, and when the wheel turns, the rod moves back and forth. This mechanism is used in many reciprocating tools.
Image by BRoys [CC BY-SA 2.5]
4) Solenoids
A solenoid is an electric coil which, when energized, either pulls or pushes an iron or steel plunger. The plunger can be spring-loaded so that it returns when the solenoid is not energized. Solenoids are used in electric locks in cars and security doors, old door bells, electrically controlled valves, and many other applications.
Perhaps the most fun application of a solenoid I’ve ever seen is in Spazzi, the solenoid-powered dance bot, created by Marek Michalowski of BeatBots. Here’s my own version rocking out to some 8-bit chiptune music.
5) Pneumatic Muscles
Soft robotics techniques are becoming more prevalent, so I’ll wrap up this list with an example from the Harvard Soft Robotics Toolkit. You can use a braided mesh tube with a skinny balloon inside and the ends clamped to create a pneumatic muscle. When the balloon is inflated, it cannot expand along its length because it is clamped to the braid. It can only expand radially, causing the braid to contract.
Source: http://softroboticstoolkit.com
You can use opposing sets of these artificial muscles to bend an arm just like in the human body, or anywhere you need to pull on something. Soft robotic actuators like this have some “give” in the mechanism. This can be essential in robots designed to work closely with humans. Soft robotics are likely to find uses in more and more personal service robots, where a traditional actuator might easily cause an injury.
ADVERTISEMENT