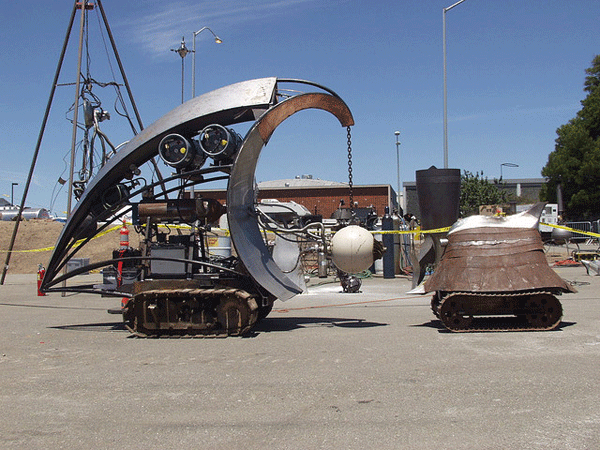
Our 7th annual Maker Faire Bay Area, taking place on May 19 and 20 at the San Mateo Fairgrounds, is definitely geared to be the Greatest Show (and Tell) on Earth, with over 700 makers to be in attendance. One maker whose creations I always look forward to seeing is Justin Gray, who has participated in Maker Faire since the first one in 2006. Justin has a gift for resurrecting and re-envisioning vintage hunks of machinery into destructo bots with an abundance of personality. They’re mesmerizing to watch as they roll and scuttle, some spewing flames. It’s hard not to smile when you see them. Justin took some time to chat with us recently.
1. When did you start building robots and how did you get into it?
I started playing with R/C cars when I was about 10 years old. Soon after, I discovered people who were radio-controlling big cars for TV and wanted to do stuff like that myself. It wasn’t until about 10 years ago that I decided to build my first actual robot. From that decision, I started playing around with experimental designs, and a couple of (failed) prototypes later I built Darwin.
2. Where do you get the parts and inspiration for your robots? What’s your R&D process like?
In some cases (like with Darwin), the artistic vision of the robot came first, then the drive systems, but that didn’t work too well since the drive systems ended up being underpowered. Now, when I find a neat vintage tracked machine dead and cheap, I pick it up and start getting ideas about an art piece around it. My current dead tracked machine yet to be art is a 1924 Cletrac Model F. The parts range from scrapyard finds to state-of-the-art electronics, motors, and batteries. The R&D process is entirely on my whiteboard and in my sketchbook. Last year’s build of Boris involved a lot of drawing and brainstorming. Boris‘ drive system was actually drafted on paper, then machined and assembled.
3. It took you 550 hours to make Boreus Hyemalis. What was the most challenging part?
Boris was an intense 60-day project. I was consumed by my work with this robot, and really, if I was any less than consumed he would not have made it into the shipping container to go to Denmark for the event he was commissioned by. The hardest part on Boris was building his independent hydraulic track drive that replaced the original Davis clutch drive system consisting of levers and clutches. Of course I had to have servo-controlled hydraulics for the tracks.
Actually, Boris being my latest robot, I was able to utilize the experience of other robots like Libby for the build. I think the most fun was stripping out all of the old mid-70s parts and making a gigantic pile of antiquated junk on the floor to be scrapped, including the original gas motor (of course Boris is electric!). What was odd for me was that I really had no plan for the sculpture portion. The only plan I had was to roll a bunch of steel tubing and start cutting and welding, seeing the final result only in the bitter end.
4. Darwin and Libby are two of my favorite pieces of yours. Tell us a bit about them.
Ahh, Darwin and Libby, also my two fondest robots. So, as you know, Darwin is my first real performance fire sculpture robot. He started from rolled sheet metal on a crappy old wheelchair platform that I got from a wheelchair supply place for free. I had no idea what I was in for in starting this robots build. Now, Darwin has scrapped his crappy 2-wheel-drive base for a voracious 60hp track drive base. If you look closely at Darwin this year you will see his brand new Struck Corp tracks underneath. Can you imagine a 600lb steel-tracked robot doing burnouts?
Libby is my darling gigantic robot. Born from the sadness of my dear dog Libby’s death, Libby (the robot) started life as a 1976 Mauldin asphalt-paving maching long since derelict and about to be scrapped by its owner but put on eBay as a parts machine. I could not resist the $300 price for a 9500lb machine. After the eBay purchase I was faced with how to acquire the platform from southern California. So I borrowed a friend’s 10,000lb-capacity trailer and headed south. Once the paving machine was in my shop I started cutting it down to the parts I really wanted: the hydraulic-driven tracks. As soon as I had the tracks isolated from the rest of the machine I was able to start visualizing Libby as a whole. It was actually a couple of years later with a small grant from The Crucible that I was able to finally build robot Libby in about a month’s time.
5. When did you start incorporating fire into your pieces and how did you learn the ins and outs?
In 1999 I met Dave Andres, Vance Cearly, and Orion Fredericks. Dave and Vance had already started doing fire in their art. Inspired by that, I began building basic fire art, then I built my first performance fire sculpture: Pressure. Shortly after that, the four of us decided to form Therm. Following the lead of Dave and Vance I was able to learn the basics of fire art and even invent a few neat things myself, like the “powder feed” systems. Dave and Vance had always used pyro chemicals in their fire art but had only simple gravity feeds into the blowers to introduce the flame colorant; on one of our many trips to the machine supply place I came up with the powder feed, allowing the operator to simply press a button to change the colors of the flame.
6. What’s your favorite tool?
Well, they say money is the sharpest tool on the bench, but that’s crap. I would say that second only to my multi-tool is my brain. I can make any tool I want.
7. Tell us about your custom fabrication shop, Graywrx Fabrications, where you make badass electric motorcycles.
I started Graywrx Fabrications in 1997 out of my garage in west Oakland. A couple years later, with a generous grant from FHA and HUD, I bought a west Oakland Victorian house with a 4-car garage on the property. I immediately converted the garage into my shop. I spent 14 great years building art and doing fabrication jobs out of my little garage. Now I have a 4000-square-foot shop in a large building in west Oakland only a few blocks from my old garage. We do all kinds of work out of Graywrx Fab, from custom hand rails and balconies to special F/X.
8. You’ve been a maker at every Maker Faire since the first in 2006. How did you first hear about it and what drives you to come back each year?
I first heard about Maker Faire through Jon Sarriugarte, who invited me to join him showing art at the very first Maker Faire. At the time it was less organized than it is today, and I happened to meet Louise Glasgow and Sherry Huss by driving Darwin with fire around the Faire and getting a stern talking to and a stern invitation to come back! Maker Faire, to me, is the mecca of art merged with technology. Every year I am inspired by the people and the work they bring to the event. For someone like me, being intellectually challenged is rare, and going to Maker Faire is like being at a buffet of knowledge.
9. What advice do you have for young makers who are inspired by your work?
I think that people who are inspired my work should decide to build and be committed to build and stop listening to the people who insist on going the normal route in life. For kids, keep playing, keep imagining, keep painting and making art.
Thanks Justin! I miss Darwin — can’t wait to see him again! For folks who want to come join us and check out Justin’s creations in person, head over to the Maker Faire website for all the information you need, including how to get tickets in advance.
And to see some of Justin’s pieces in motion, check out a video of him at last year’s Maker Faire Bay Area:

See you there!
ADVERTISEMENT