I restore antique radios to make the cash I need to play with my toys. Audiophiles are happy, so is my wallet.
Mainly we do this simply because the ‘original’ parts are no longer available, or if they are, the price is exorbitant.
Project Steps
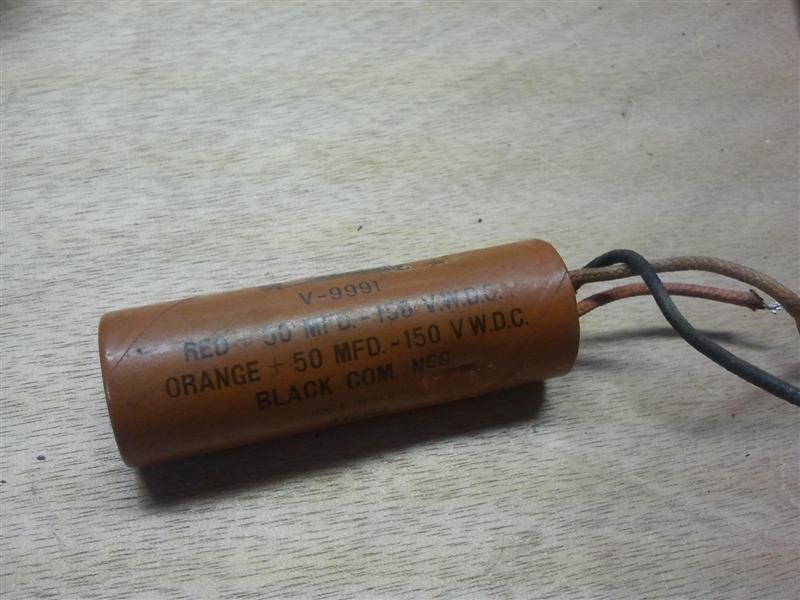
When working in an old TV, Audio Amplifier, or Turntable, invariably I will run across capacitors of all types, Paper, mica, electrolytic, etc…. Generally when we run into caps that are of the electrolytic type they are mostly dry, or drying out. Some common practices have people just shotgunning the problem by swapping out all old caps with new technology.
Electrically equivalent…..but to some of my audiophile buds, it is blasphemy bordering on the obscene. It should also be noted… with times being what they are… You can command a little bit more for the units you choose to sell noting no new tech parts are there.
Let’s start off with the offending part. A dual cap 50uf@150wvdc in a waxen pressed board container.
Nicely, notice I did not use the word gently… Smiley Take an old soldering iron and use it to liquefy the resin and waxen plug in the end of the cap. Some liquid will co-operate and gently flow out, the rest will become soft like putty, and easily manageable with the tip of a small flat screwdriver. NOW, gentle heating with a HAIR DRYER will loosen the material near the wall, and then clean it with the screwdriver. When you get to them, cut the cap leads at the rivets. (You will see them and feel them with the melting iron)
When you get deep enough, take soldering iron and press it into the center of the old cap material. This will make a pilot hole.
Take a 3/8th’s drill and while holding the cap shell by the side, measure (with the drill bit) how deep you can go, less about 3/4″ just for safety, and mark it with some tape . Now, take the cap and hold it with gloves or whatever you feel comfortable with… and gently drill into the cap materials. If you go slowly, the drill SHOULD take a grab onto the whole core when it gets into the upper resin and the whole core SHOULD spin in the cap barrel. STOP drilling when you get to the tape mark or the core spins.
Now grab the core with a hooked dental pick, o-ring tool, or even a small bit of wire with a slight hook in it. Pull out your prize.
Here are your 5 constituent parts of the cap, less the plug material.
Now, here comes the fun part. Take the replacement value caps, for ME, alone, I used three 25uf@250v caps per side of the cap. Remember, CAPS IN PARALLEL ARE ADDITIVE, while keeping the working voltages the same. Yes, I purposely chose 3 caps because they will form a triangular pattern for better centering. I put a large loop on these negatives, since this will be the common point for the cap.
Cap bundle with the positives wired and the rest is now the pigtail for one of the positive leads.
Needed to be done twice. Leave enough wire on the second bundle to hook them together.
Take the negative lead from the second cap, and feed it through the center of the first cap, and cut it long enough to hook it to the first bundle’s loop(remember that?)
Remove the second cap bundle. Take some black tape and put a layer or two on the top of the first bundle. Poke a hole in it with the tip of a soldering iron.
Reassemble the two cap bundles, soldering the negative lead from the second bundle, and the black(or whatever color it is) to the lug on the first bundle. Attach the remaining original wires to the positive leads.
Now, insert the whole new stack ‘o caps into the old shell. Take a moment to admire your work.
(no pics of the next 2 steps) Cut out a small piece of gray cardboard . The annoying fiberboard most things are shipped in or used as card material. Cut it down to the size of the inside of the cap shell. Poke 3 small holes for the leads. Feed the leads through the holes and press the fiber circle into the cap body, pushing it in about 1/2″.
Take your melting iron, and using a small candle(unlit) preferably white, but not a brilliant white, melt the bottom of the candle filling in the bottom of the cap body. This is simply for aesthetics, but what the heck. Don’t be lazy and burn the candle to drip. There is conductive carbon in the dripped wax.
Tahdah! A brand new ‘antique’ cap. Take a second moment to chuckle.
Re-inserted into the radio/amplifier. Smile knowingly to yourself.