I wanted a way to build rigid, strong, high-precision objects that are much larger than I can cut in my personal laser cutter. In response, I designed Lightbeams — which I’m now turning loose in the world.
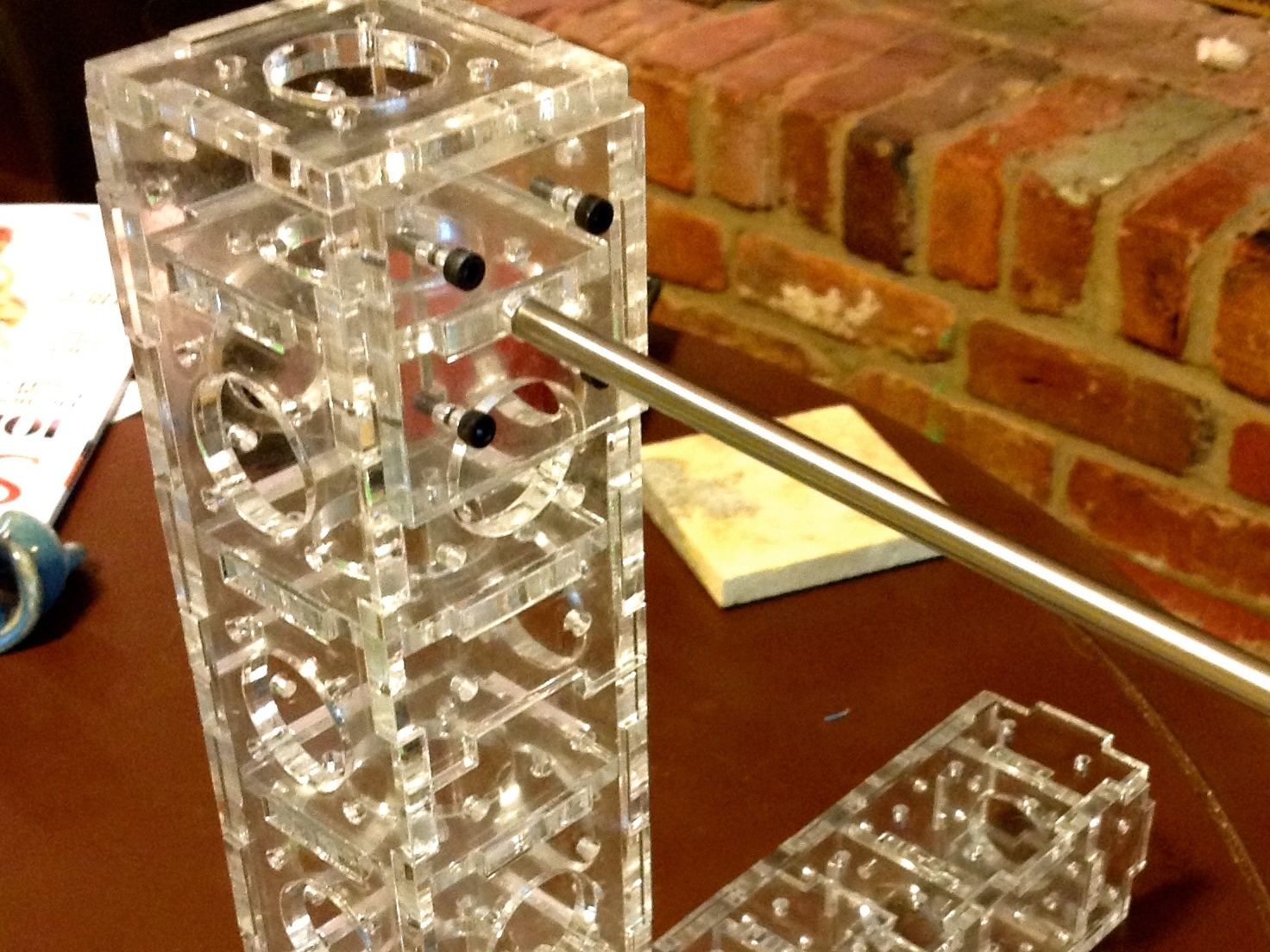
I have small laser cutter (40W Full Spectrum Engineering Hobby Laser). I generally feed it wood or acrylic in 8″x12″ chunks. However, I’d really like to make things that are much bigger than that — like my next 3D printer. I want to design a printer that is bigger, more rigid and with tighter tolerances than my current Cupcake-derived model.
My solution was to design a rigid, extensible structural framework based on 0.22-inch acrylic. Since they’re clear AND made on a laser, I call them “Lightbeams”.
Each beam is formed from a basic repeating “1U Girder pattern”. You can see it pictured here.
It’s designed so that you get nice repetition of the mounting holes in all three dimensions.
I wanted to do this in metric (really America, get out of the Middle Ages!), but I live in the U.S. and have many fewer choices in materials (such as steel rods of a given length) if I use metric. Fortunately, this system is easy to use with metric bits as well.
Doesn’t look like much as a single unit, but it took me nine iterations to get here!
By repeating the 1U basic form we can now make interesting components.
This one is a 4U Girder side. The small holes repeat every inch and can be used as mounting points for whatever you need to attach to the Lightbeam. The big holes allow you to route wiring or anything else through the interior of the structure.
The rectangular cutouts allow us to add “girder cores” to the system that keep it very rigid and square.
And here is just such a Girder Core!
The 4 little mounting holes allow you to mount electronics or other items INSIDE the beam if you so choose.
They also allow you to connect beams to one another at right angles as this core piece also forms the end cap on one end of the beam (I tried to reduce/reuse/recycle parts wherever possible to reduce the number of unique parts required to build things).
The big hole in the center allows wiring or other “stuff” to route through the center of the beams.
Here’s how a beam is built! Just glue the parts together with homemade acrylic cement.
Homemade acrylic cement? Oh… just dissolve all your waste acrylic bits in acetone to make a thick glue. Welds acrylic together and is virtually free!
By staggering 2U sides and 4U sides you get a very strong beam. The core pieces make this very square and very rigid.
The Cores are also the “male” end caps for a beam. One part, two functions.
This works really well because the screw holes and the main hole in the cores/ends match the spacing of those on the side of a girder. This means you can bolt an end cap onto the side of a girder to make a right angle between two beams.
The alignment of the big hole also means you can run wiring from one axis into another within the beam.
Note: the vertical beam pictured was a prototype that does not include all the routing holes.
From this basic system it is very easy to create any kind of mounts you might need for whatever you wish to build.
Pictured is a linear motion rod salvaged from an old printer. The rod is held tightly simply via a compression fit.
All you need to do is make sure your 1/8-inch diameter screw holes form a square one inch on each side.
If you build a structure for linear motion using Lightbeams, rods spanning your structure will be extremely parallel even over several feet of run.
So that’s the basic overview. Use the system to make 3D printers, CNC frameworks, robotics or whatever else you might need!
It took quite a few prototypes to get this far (see the picture?), but we can go much, much farther!
Add to the system! Like everything here, the license on this is Creative Commons share-alike by attribution. Put simply, do whatever you want with it but (a) give credit where credit is due and (b) any modifications or additional modules you create for the framework you must share back in the same way. Basically: play nice!
ENOUGH TALKING! WHERE DO I GET THE FILES???? Easy… get them here: http://www.kevingunn.org/lightbeams/
How long your project takes and the materials required completely depends on what you plan to do with it! Big structures = lots of material!