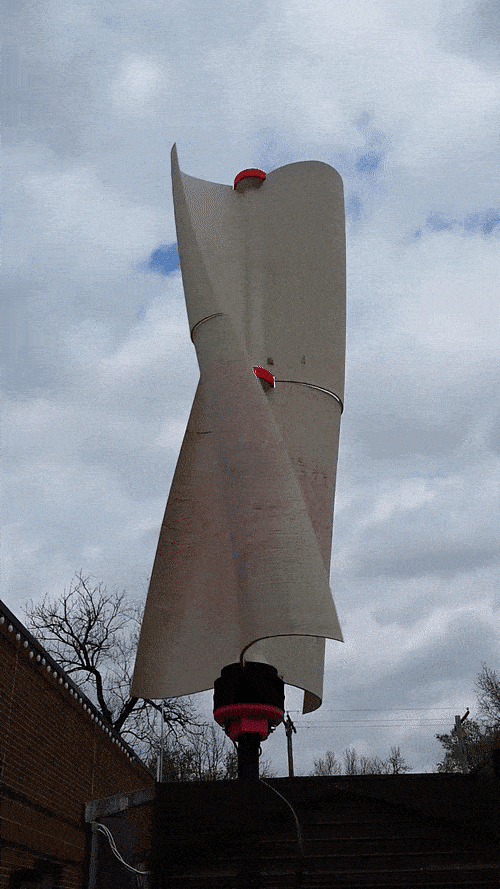
A couple of years ago, Michael Curry, former 3DP Evangelist at MakerBot and a member of Kansas City’s Hammerspace, built a 3D printed wind turbine at the space. Dubbed the Whirlygig, it’s been happily freewheeling away on the fence outside of Hammerspace ever since. Recently, Michael decided to try putting it to work by adding a generator.
Michael was interested in experimenting with two different approaches to capturing the energy from his 3D printed axial turbine Whirlygig. He wanted to try 3D printing the parts for his own homebrewed alternator and re-purposing an old 3D printer’s stepper motor to use as a generator.
The 3D printed alternator seemed like a good idea at the time. Michael writes:
Being an overachieving DIY Maker guy, naturally my first thought was to dive in and build my own 3D Printed three phase alternator. With information gleaned from DIY wind turbine websites, I set out on a quest of electromechanical discovery.
The Alternator used 9 coils of 22 gauge copper wire wound around 3D Printed cores and pressed into a supporting disk. The coil’s are connected in alternating set of three to create a phase.
The resulting alternator looked lovely, but wired up and mounted on the turbine, it performed very poorly. Microvolts poorly. So it was on to the stepper motors.
We set up a quick bench test. An Adafruit NEMA 17, 2 bridge rectifiers, a multimeter, capacitor, lightbulb, and power drill. The theory is, we’ll spin the NEMA 17 with the power drill, which will produce an alternating voltage in each of the two coils. The rectifiers will convert the voltage to DC, charging the capacitor and lighting the light bulb. The capacitor smooths out the incoming voltage, so the multimeter can get a more stable reading of the voltage being produced.
The results of the drill tests were very promising, generating up to 60 volts, so Michael began work on designing a generator using the stepper:
I settled on a somewhat Rube Goldberg solution. A spinning rain hood/internal gear that is spun by the turbine on a bearing ring of ½ inch delrin spheres. Inside the rain hood, a toothed internal gear meshies with a drive gear on pressed onto the stepper motor. As the turbine spins the rain hood, the gearing will spin the spin the stepper with about a 4:1 speed advantage. The delrin bearings keep everything spinning freely while keeping the teeth of the gears engaged with each other.
Hooking the resulting generator up to the turbine, Michael was able to get 9 volts out of it with only a light breeze. He is now thinking about where to take things next and what he might do that is useful with the power the mill is generating.
You can read more about the generator project here. And read the backstory on the 3D printed Whirlygig, here.
ADVERTISEMENT