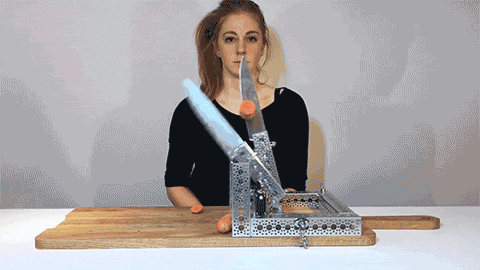
Tired of all those hours spent chopping vegetables in the kitchen? Are you looking for a fast and effective way to separate your fingers from your hand? Well then, check out Simone Giertz’s Chopping Machine. Her combination of kitchen knives and continuous servo motors is quite possibly the most reckless and dangerous (and arguably idiotic) project we’ve ever written about. And while we’d never build one (nor recommend that you do), we can’t take our eyes off it.
Giertz has a knack for building ridiculous, impractical contraptions. From her toothbrush helmet or face-slapping alarm clock, to her cereal-feeding robot. Pitched on the idea of creating a helpful gadget for the kitchen, Giertz naturally thought of affixing a motor to the biggest knife she could find. The result is a nightmare-inducing chopping machine that chops vegetables into (somewhat) smaller bits before flinging them off the table.
Though we in no way encourage you to make one of your own (please, seriously, don’t), here’s what she used to create this tabletop carrot torture apparatus. The knives are attached to a pair of Hitec HS-7950TH ultra-torque continuous servo motors, mounted to a ridiculously large cutting board using Actobotics aluminum channels. An Arduino Nano does the servo math, seemingly programmed with a predictable delay so that you can place items on the cutting board without losing a limb.
Filming my next project! Out this Wednesday, stay tuuuuneeeed ❤️ pic.twitter.com/KhPLRShwLe
— Simone Giertz (@SimoneGiertz) December 12, 2015
I asked Simone about any challenges she may have had getting the servos to reliably chop and she had this to say:
I got the Hitec servo motors working after doing some math! Apparently the motors I used could only read PWM signals that were between 0.9ms and 2.1ms. The Arduino Nano’s can send PWM pulses that are a lot shorter than that, so anything that was too quick for the motors to read just got interpreted into random chopping. 0.9ms pulse length correlates to analogWrite(115) so I just used values between 115–255 for the PWM instead of 0–255 and the motors started acting right!
I didn’t read up on continuous servo motors properly, I just really wanted to believe that they would give me full position control (which is preferable when you have the motors decide when two very sharp knives will fall) at the same time as they could spin all the way around. Continuous servo motors shouldn’t get to be called servo motors at all since they have none of the position control you’d expect from a servo motor… But it worked out pretty well in the end anyway! I still have all ten fingers left and was forced to learn a lot about servo motors and PWM signals so I’m not complaining.
ADVERTISEMENT